Copper wire diameter does not meet national standards = non-standard cable? Authoritative interpretation subverts industry cognition!
The qualified standard of a cable is hidden in the resistance value rather than the copper wire diameter. The report of China Quality Certification Center is quietly changing the industry’s judgment logic of “non-standard”.
In the wire and cable industry, a controversy that has lasted for decades has troubled manufacturers and purchasers: when the copper wire diameter is less than the national standard nominal value, is it an unqualified “non-standard” product?
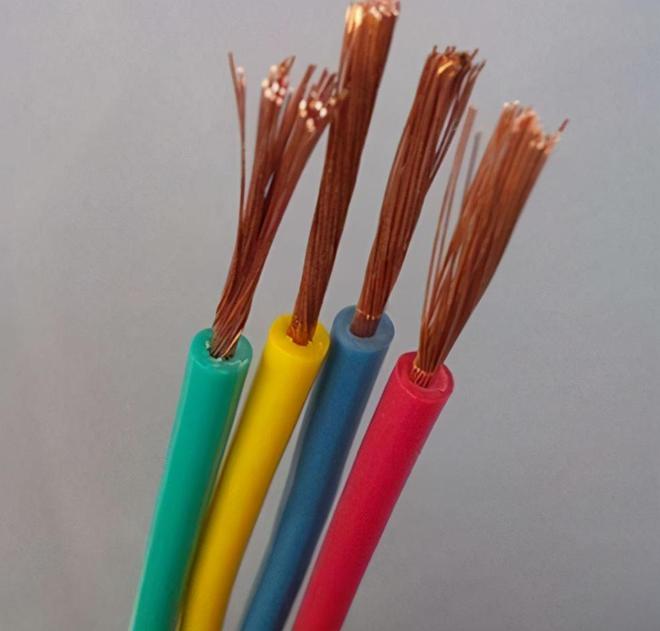
Many customers are accustomed to using micrometers to measure the conductor diameter as a basis for acceptance, and even in engineering acceptance, it is common to see technicians holding calipers to measure the copper wire diameter. However, the authoritative report of the China Quality Certification Center (CQC) gave a subversive conclusion: Whether the cable is qualified depends on the conductor resistance value, not the cross-sectional area**.
The national standards GB/T 5023-2008 and GB/T 12706-2008 clearly stipulate that cable conductors meet the requirements of GB/T3956, and the main assessment indicators are only two: the maximum single-wire diameter of soft conductors (or the minimum number of single-wires of hard conductors) and the conductor resistance value at 20°C. The standard does not set a lower limit for the actual cross-sectional area of the conductor.
1. The core of the national standard, the truth of resistance rather than diameter
The national standard GB/T 5023-2008 clearly defines: For BV 2.5mm² cables, the type test only requires a maximum resistance of ≤7.41Ω/km at 20°C and a maximum outer diameter of 1.9mm. The nominal cross-sectional area is only a specification code, which is used for production management and document identification.
The mainstream standard system for wires and cables (IEC, European standards, and national standards) all assess different cross-sectional specifications through conductor resistance values, rather than actually measuring the conductor cross-sectional area. When the purity of copper material is improved, even if the diameter is reduced to 1.75mm (theoretical cross-section 2.40mm²), as long as the resistance value meets the requirement of 7.41Ω/km, it is still a qualified product.
This phenomenon stems from the progress of materials science. The popularization of oxygen-free copper production technology has significantly reduced the resistivity of copper conductors, and copper wires with a diameter smaller than the nominal diameter can fully meet the DC resistance requirements.
In the GB 50217-2018 power cable design standard, the China Electricity Council has strengthened the core position of resistance performance and further weakened the traditional mechanical assessment of cross-sectional area.
2. Industry misunderstandings and costs, when diameter becomes the only standard
There is a worrying situation in the cable industry: more than 40% of companies have encountered low-cost bids and malicious price-cutting bidding. In a market environment with an overcapacity of 60%, price wars have forced some companies to cut corners, and “non-standard” products are rampant.
The “simple method” of measuring diameter has become the mainstream judgment method, but this seemingly rigorous approach actually deviates from the essence of national standards. When the purchaser only uses calipers to judge the quality of cables, it creates a living space for real non-standard products – those products using impure copper and recycled plastics may pass because of “diameter compliance”.
What’s more serious is that diameter worship conceals key safety hazards. Qualified cables must ensure that the insulation thickness meets the standard (such as 2.5mm² insulation layer thickness ≥ 0.8mm), but simply measuring the diameter of the copper wire cannot identify insulation defects. When designers reserve a surplus according to the nominal cross-section, the cable with a discounted wire diameter will offset the safety margin and may cause overload accidents during peak power consumption.
3. Authoritative testing and standard evolution, CQC report interpretation
As a national certification body, the China Quality Certification Center (CQC) made a clear statement in the report released in 2023: The phenomenon of qualified DC resistance and wire diameter less than the nominal value meets the product standard. This conclusion is based on the assessment system of GB/T 3956, which is included in the latest version of GB 50217-2018 power engineering cable design standard.
The trend of standard evolution is clearly visible. New regulations such as JB/T 10437-2024 “Cross-linkable polyethylene insulation materials for wires and cables” to be implemented in October 2024 continue the concept of electrical performance as the core. Professional testing method requirements: When the conductor resistance is measured at a temperature of 21.7℃ and is 7.39×10⁻³Ω/m, it needs to be converted to 7.34Ω/km at 20℃ as the basis for judgment.
The scientific nature of resistance measurement lies in its comprehensive reflection of material purity and structural integrity. As industry experts said: “Products with a wire diameter of 1.75mm but qualified resistance are much safer than products with a wire diameter of 1.78mm but using impure copper.”
4. The true definition of non-standard cables, distorted concepts and hazards
The so-called “non-standard” in the industry has deviated from its original meaning. Initially, “non-standard” refers to products customized on the basis of standard products according to the special needs of users, which belongs to the category of legal production. But now, non-standard has become synonymous with counterfeiting and shoddy products.
Real non-standard cables are manifested in three forms:
- Length fraud: “jumping meters” means (nominal 1000 meters, actual payment 900 meters)
- Material substitution: using ordinary materials to replace high-temperature resistant insulation materials, or using recycled waste plastics
- Brand fraud: counterfeiting well-known brand packaging
The harm of these products is far greater than that of qualified cables with insufficient diameters. The counterfeit copper core is purple-black or yellowish, with high impurity content, poor mechanical strength and easy to break. A simple white paper test can identify it: black residue appears after rubbing the copper core with white paper, indicating that the copper impurities exceed the standard.
5. The root cause of industry chaos, the survival dilemma under low-price competition
As a typical field of “heavy materials and light work”, the wire and cable industry has raw material costs accounting for more than 80% of the total cost. When copper prices fluctuate, the profit margin of enterprises is greatly compressed. More than 7,000 production enterprises compete for a limited market, forming an industry norm of “small profits or even losses”.
Low-price bidding triggers a vicious cycle. An industry survey shows that some companies bid at a price 40% lower than the cost price in order to win the bid. After winning the bid, they can only survive by “70% off the wire diameter” (70% off the diameter) or reducing the amount of copper used. The plight of a fire-resistant cable manufacturer in Tianjin is very representative: the shutdown during the epidemic period led to a backlog of high-priced copper raw materials, and the capital chain was on the verge of breaking.
Return to the essence of quality to solve the dilemma. The centralized procurement system and unified management of raw material prices promoted by the state are guiding the industry from price competition to quality competition.
6. How consumers break the dilemma, and the five-step identification method protects their rights and interests
Faced with market chaos, consumers can use a systematic method to distinguish the authenticity:
- Check the label: Check the quality system certification, factory name and address, production date and voltage specifications. Any missing item is a suspicious product. The national standard GB/T 5023.1-2008 has mandatory regulations on labeling.
- Bending test: Take the wire head and bend it repeatedly. High-quality products feel soft and have no cracks in the insulation layer, while inferior products are easy to break.
- Weight verification: The standard weight of 1.5mm² cable is 1.8-1.9kg per 100 meters, and 2.5mm² is 3.0-3.1kg. Insufficient weight indicates that the length is short or the copper core has too many impurities.
- Copper quality inspection: Peel off the wire head and observe the copper core. Qualified products are purple-red and shiny; black or white contains impurities. White paper rubbing test can be further verified.
- Price comparison: Products that are significantly lower than the market price need to be highly vigilant. The industry consensus points out that “cables that are 20% lower than the normal price have a sharp increase in non-standard risks.”
In case of disputes, they can be sent to a third-party agency for inspection. Only the 20℃ conductor resistance test can be used to determine the core quality.
The wire and cable industry is undergoing a cognitive revolution: Insufficient copper wire diameter does not necessarily mean non-standard, and resistance value is the core criterion. With the popularization of CQC reports and the implementation of national standards GB 50217-2018, this change is spreading from the technical level to market cognition.
Data from the market supervision department show that in 2024, among the complaints about cables that were misjudged due to “diameter not meeting the standard”, 83% were confirmed to be qualified by resistance testing. When consumers learn to use electronic multimeters instead of calipers, and when professional inspections are used instead of naked eye judgments for project acceptance, the cable market can truly achieve “good money drives out bad money”.
National Standard Full Text Publicity System: GB/T 5023-2008 China Quality Certification Center Official Website: CQC Report Query