Cutting corners on wires and cables: a deadly threat hidden in home decoration
A copper wire that is 5 cm shorter and an insulation layer that is 0.1 mm thinner are quietly sowing the seeds of disaster inside your home wall.
Wires and cables are the “blood vessels” of the home electrical system, and they undertake the key task of transmitting electrical energy. However, about 30% of the cables on the market are non-standard products, and the price is 10%-40% lower than the national standard, which buries fatal hidden dangers through cutting corners. These inferior cables are like time bombs, which continue to threaten family safety for months or even years after the decoration is completed. When high-power electrical appliances such as induction cookers, air conditioners, and refrigerators are turned on at the same time, the hidden dangers may erupt into irreversible disasters.
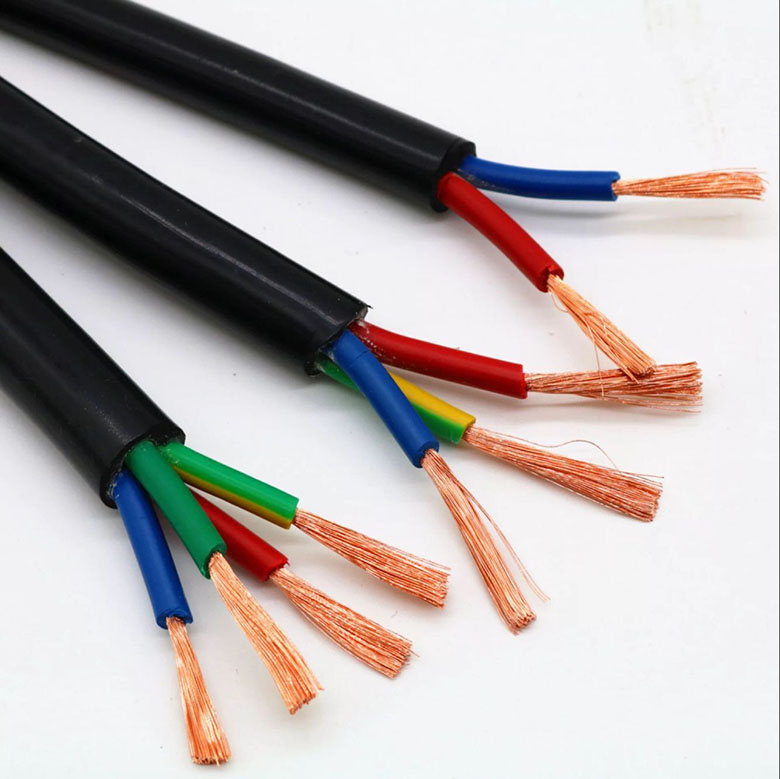
1. The creation of invisible killers: the main form of cutting corners
The cutting corners of wires and cables presents industrialized and hidden characteristics. A survey of the largest hardware market in South China shows that non-standard cables generally reduce the number of copper wires from 32 to 26, resulting in a reduction of nearly 20% in the conductive cross-sectional area.
Even more dangerous is the counterfeiting of the insulation layer – the material that should withstand a high temperature of 70°C is replaced with an inferior plastic of 65°C. Once the current is overloaded, the insulation layer will quickly melt and cause a short circuit.
In the random inspection by the Beijing Municipal Administration for Industry and Commerce in 2017, the thinnest point thickness of the insulation layer of a certain company’s cable was seriously insufficient. This deliberate reduction of the key protective layer has increased the risk of wire exposure.
The test results of a third-party testing agency are even more shocking: the national standard requires that PVC insulated cables should not be broken down for 5 minutes under a voltage of 2500 volts, but non-standard products are broken down and catch fire in just a few seconds.
2. Hotbed of flames: the root cause of fire hazards
Excessive conductor resistance is the most fatal defect of inferior cables. When the resistance exceeds the national standard by 35%, a large amount of electrical energy will be converted into heat energy. Imagine: in a closed wall environment, when the air conditioner and electric water heater are turned on at the same time, the inferior wire is like a gradually red-hot iron wire, and the temperature can reach over 100°C.
The insulation layer softens and falls off at this high temperature, eventually causing a short circuit and sparks, igniting the surrounding wood and insulation materials. Zhujiang Cable’s safety analysis pointed out that more than 38% of home fires are caused by electrical line problems, among which insulation failure caused by cutting corners is the main cause.
The “Okai Cable Incident” in Xi’an Metro is a real warning – although the official argued that it was “only used for auxiliary systems”, professional institutions confirmed that its insulation layer failed to meet the heat resistance and flame retardant performance requirements, forcing the government to replace the entire line cable overnight.
3. Silent destroyers: equipment damage and electric shock risks
The hazards of inferior cables are far more than fire. Insufficient conductor cross-sectional area will cause abnormal voltage fluctuations, just like letting electrical appliances “work with illness”. Air conditioning compressors repeatedly start and stop under low pressure, shortening their lifespan by more than 30%; precision electronic products such as computers and smart home hosts are more likely to burn out motherboards due to instantaneous surges.
A more hidden threat is leakage. The Beijing Industry and Commerce Bureau’s notice revealed that shoddy cables are prone to cracking during installation due to uneven thickness of the insulation layer, exposing the copper wire. When humid air penetrates the wall, the metal conduit may be instantly electrified. Tests show that the breakdown voltage value of non-standard cables is less than 1/3 of the national standard, which means that ordinary humid environments can cause leakage, which can cause tripping at the least and electrocution death in the shower at the worst.
4. Double trap: fatal misunderstandings in the construction process
Even if qualified cables are selected, incorrect construction methods will also amplify the risks. Chancheng Cable’s research found that four major laying errors are common in home improvement construction sites:
- Combined management of strong and weak electricity: The network cable and the power cable are placed in the same tube, and the current interference causes signal disorder, and the heat accumulation accelerates insulation aging
- Direct buried wires without casing: In order to save labor time, the bare wires are directly buried in the wall, and the cement erodes the insulation layer and leaks electricity
- Repeated wiring: Only 1-2 wires are placed in a single tube, which is wasteful and increases the number of fault points
- Mixed connection of aluminum and copper: In the renovation of old houses, aluminum wires and new copper wires are directly twisted, and the oxidation reaction causes a surge in contact resistance, and the temperature at the joint can reach 150℃
These practices are essentially another form of “cutting corners” – The construction party reduces costs by cutting processes, and the owner ultimately bears the safety hazards.
5. Build a solid safety line: full chain protection from purchase to supervision
(I) Four-step method for consumer self-protection
- Recognize the identity mark: Check the CCC compulsory certification (the serial number can be verified on the China Electrical Certification Network) and the production license number, and reject “three-no” products without factory name and address
- Measure the conductor quality: Cut the wire head and observe the copper core – the national standard requires bright oxygen-free copper with a copper content of 99.99%. If it is dark or has impurities, it is a low-quality product
- Verify the length tolerance: The national standard allows an error of ±0.5 meters per 100 meters, and the outer diameter of the entire roll can be measured (such as the outer diameter of the nominal 2.5mm²×100m wire should be ≥68mm)
- Request for test report: Request the merchant to provide a recent resistance and withstand voltage test report (preferably issued by a provincial quality inspection agency)
(II) Supervision strikes hard
After the Xi’an Aokai incident, the government included cables in the key supervision category and took measures such as flight inspections and random inspections in the circulation field to combat counterfeiting. When consumers find suspected non-standard products, they can report to the 12315 platform and claim compensation in accordance with the “Product Quality Law”.
VI. Systematic solutions: corporate responsibility and technological innovation
To eliminate cutting corners, it is necessary to break the source of the industrial chain. High-quality companies such as Zhujiang Cable set a benchmark through the triple protection system:
- Raw material control: Using Jiangxi Copper’s 99.99% oxygen-free copper to ensure conductivity from the source
- Process innovation: The insulation layer uses flame-retardant PVC, which does not deform after a high temperature test of 90°C
- Traceability management: Each roll of cable is printed with a traceability QR code, including production batch and inspector information
In 2025, Zhujiang Cable launched the “Smart Quality Control” project, implanting an AI quality inspection system in the production line to monitor outer diameter deviation and insulation extrusion density in real time.
The essence of cutting corners in wires and cables is a deadly deal of “exchanging safety hazards for profits” – shortening the copper wire by 5% may increase the probability of fire by 50%, and reducing the insulation layer by 0.1mm may mean a 30% increase in the risk of electric shock.
As household electricity load increases year by year with the popularization of smart home appliances, only by choosing national standard cables, standardizing construction, and regular testing (it is recommended to measure the insulation resistance with a megohmmeter every 2 years) can this “electric wall” be built into a real safety barrier.
Ms. Wang, a Beijing citizen, still remembers the summer of 2017 – when the Industrial and Commercial Bureau announced the list of inferior cables, she found that she was using one of them for her home decoration. After testing, it was shown that the thinnest part of the insulation layer was only 0.4mm, which was lower than the national standard lower limit of 0.6mm. The cost of demolishing the wall and reinstalling it was 27 times the price difference saved at the beginning.
Appendix: Common forms of cutting corners and hazards in wires
Corner-Cutting Method | Technical Indicator Change | Potential Hazard | Real-World Case |
---|---|---|---|
Reduced copper wire count | 32 → 26 wires (-18%) | 35% resistance increase, sharp temperature rise | Non-standard cables (Guangzhou-Foshan Hardware Market) |
Thinned insulation layer | Thickness: 0.6mm → 0.4mm | 60% reduction in breakdown voltage | Incident report (Beijing Kunlun Cable) |
Recycled plastics replacing new materials | Temperature resistance: 70℃ → 65℃ | Increased softening and leakage risks | Xi’an Aokai Metro Cable |
Insufficient cable length | Labeled 100m → Actual 92m | Frequent failures due to excessive joints | 3.15 Expo short-weight cables |