Wire aging: the hidden electrical killer! Comprehensive analysis of the six major causes and scientific detection solutions
Wire aging is like a time bomb lurking in the wall. Every electric spark may trigger an irreversible safety accident.
Wires and cables play the role of “blood vessels” in power transmission, and their performance degradation directly threatens the life of the entire electrical system. With the increase in service life, **wire aging has become the main cause of electrical fires, accounting for about 30% of all electrical fires.
In high temperature and high humidity environments, the **insulation performance of ordinary cables may decay by more than half in just a few years, and the naked eye is often difficult to detect this fatal change. What is more alarming is that cables that have been in operation for about 20 years in Shanghai have entered a period of frequent accidents. Studies have shown that there are a large number of “bow tie-shaped water branches” in these cables-a dangerous signal of accelerated deterioration of insulation performance.
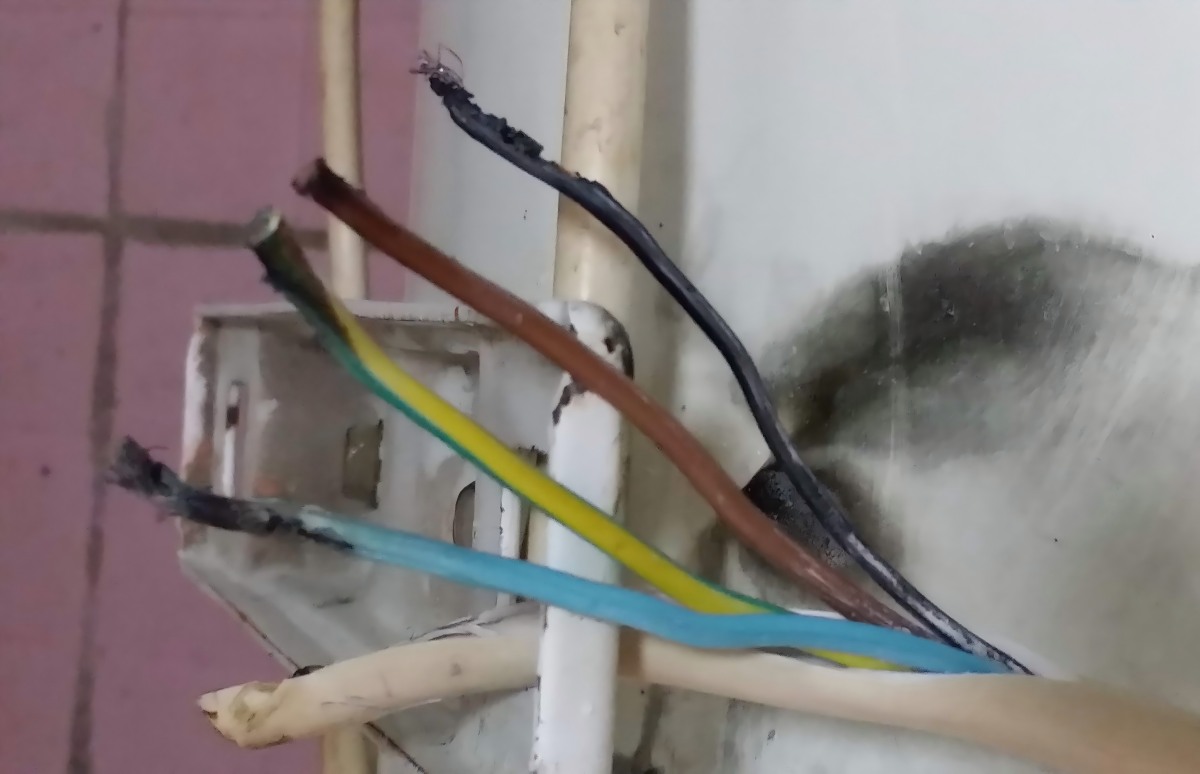
1. Six major causes of wire aging
Wire aging is not a simple sign of time, but a complex process of multiple destructive factors intertwined:
- The invisible threat of external damage: In the rapidly developing Pudong area of Shanghai, mechanical damage is the primary cause of cable failure. Irregular construction and civil engineering work on directly buried cables will cause “internal injuries” to the cables. These injuries may lurk for months or even years, and eventually evolve into insulation breakdown or short circuit failures. Just like internal bleeding in the human body, the appearance seems intact, but the inside is full of dangers.
- “Water branches” erosion in humid environments: Cable joints in direct burial or drainage pipes are very likely to become breakthroughs for moisture erosion. Unqualified joints are made in humid climates, and after water infiltrates, they form tree-like erosion channels under the action of the electric field – professional terminology is called “water branches”. These “branches” are like conductive paths opened in the insulation layer, continuously weakening the insulation strength of the cable.
- Silent attack of chemical corrosion: Cables buried in acid and alkali areas face the fatal threat of chemical corrosion. Armor, lead or outer sheath gradually fail under chemical corrosion or electrolytic corrosion, and the insulation strength of the unprotected cable plummets. The corrosion cases of cables in chemical zones are particularly alarming – the corrosion rate is far higher than that in normal environments.
- Thermal damage caused by overload operation: When the current exceeds the designed capacity, the heating of the conductor, the eddy current loss of the steel armor, and the loss of the insulating medium work together to cause the cable temperature to rise abnormally. When the overload operation is carried out for a long time, high temperature will accelerate the breakage of the molecular chain of the insulating material, resulting in insulation embrittlement. In the hot summer, this thermal damage is particularly prominent, and the cable failure rate increases significantly.
- The weak link of the cable joint: The most vulnerable part of the cable line is the joint, and about 40% of the cable failures are caused by this. The insulation performance of the cable head will be greatly reduced if the joint is not crimped tightly or heated insufficiently. Technical errors of construction personnel often bury major hidden dangers in this link.
- The catalytic effect of ambient temperature: The external environment and heat source will cause the cable temperature to exceed the safety threshold. When the working temperature increases by 8-10℃, the life of the insulation material will be halved. In a high temperature environment, this thermal aging effect accelerates exponentially, eventually leading to insulation breakdown or even explosion and fire.
2. Scientific detection methods for wire aging
Facing the hidden threat of aging, modern electrical technology has developed a variety of accurate detection methods:
- Insulation resistance test-basic health screening: Using megohmmeter (shaker) to measure insulation resistance is the most basic detection method. When measuring, the power supply of the object to be measured must be disconnected, the “E” end must be connected to the ground wire, and the “L” end must be connected to the object to be measured. It is worth noting that when there is leakage current on the surface of the object to be measured, the protection ring terminal “G” must be used to eliminate the error-this is particularly critical for insulation testing between cable cores and shells.
- Ground resistance test-safety barrier detection: Select two-wire method, three-wire method or four-wire method for ground resistance testing according to environmental characteristics. In densely populated areas, the two-wire method uses a known grounding point (such as PEN) for measurement; and the four-wire method, with its high-precision characteristics, can eliminate the influence of the resistance of the measuring cable itself, becoming the gold standard for ground resistance measurement.
- Heat aging and damp heat aging test – accelerated life test: Professional organizations such as STT Set Testing conduct heat aging tests by placing the cable in an environment higher than the normal working temperature to observe the phenomenon of the insulation layer becoming hard and brittle. The damp heat aging test simulates a humid and hot environment, places the cable in a high temperature and high humidity box, and monitors the deterioration phenomena such as water absorption and expansion, delamination and blistering of the insulation layer.
- Light aging and ozone aging test – environmental adaptability verification: Ultraviolet irradiation simulates the effect of natural sunlight on the outer sheath of the cable. The ozone aging test is aimed at rubber cables, and the material’s ozone resistance is evaluated by observing the cracking of the sheath. These tests are particularly important for cables exposed outdoors.
- Mechanical properties and chemical analysis – microstructure exploration: Tensile test detects the change in the elongation at break of the cable after aging, which is direct evidence for evaluating the degree of embrittlement of the insulation material. Fourier transform infrared spectroscopy (FTIR) reveals the degree of oxidation and fracture of the molecular chain of the insulation material by analyzing indicators such as the carbonyl index.
- Water tree observation and dielectric spectrum test-invisible killer revealed: Professional laboratories directly observe the growth of water tree through microscopes**, and use dielectric spectrum test to analyze the change of insulation medium loss. The research team of Shanghai Jiaotong University confirmed the significant correlation between water tree content and tensile strength through the analysis of more than 300 aged cables, providing a scientific basis for comprehensive diagnosis.
3. Prevention and management strategies
A systematic defense strategy is needed to combat the aging of wires:
- Establish a periodic detection mechanism: Important facilities should be professionally inspected every 1-2 years, with special attention to hidden sections such as direct burial and drainage pipes. The inspection should include basic tests such as insulation resistance and grounding resistance, as well as inspections of weak points such as joints and terminals. Regularly remove debris and vegetation around the line to prevent extrusion damage.
- Select high-performance cable materials: WDZ-BYJ low-smoke halogen-free cable is used in special environments such as humid and chemical industries. Its flame retardant properties can suppress the spread of fire in the event of a fire, and no toxic smoke is produced when burning. High-temperature resistant cables (such as 105℃ grade) are suitable for high-temperature areas.
- Standardized installation and protective measures: Protective tubes are installed on the outside of the cable to resist mechanical damage and chemical corrosion. The joints must be made in a dry environment and waterproof treatment that meets the standards must be used. Keep the cable channel dry to avoid forming a “hot and humid steamer” environment.
- Load monitoring and temperature control: Install smart meters to monitor line loads in real time to prevent long-term overload operation. Temperature sensors are added in high-temperature areas to automatically alarm when the cable temperature exceeds 65°C. If necessary, install cooling systems in cable-dense areas.
- Replace aging parts in time: When the detection finds that the insulation resistance drops by more than 30% or the tensile strength loses more than 25%, it must be replaced immediately. For cables that have been in operation for more than 15 years, the detection frequency should be increased even if the test data is normal.
- Application of intelligent monitoring technology: Adopt a state assessment system based on a fuzzy clustering diagnostic model, integrating multi-dimensional data such as water tree content, tensile strength, and activation energy. The cable state assessment and aging trend management system developed in Shanghai has achieved an accurate portrayal of the insulation aging state, breaking through the traditional judgment limitations that rely solely on commissioning time.
While inspecting a 30-year-old building, electrical engineer Li Ming found that the insulation layer of the cables in the electrical box was as brittle as thin paper. Through the megohmmeter test, the insulation resistance value dropped to 0.5MΩ-far below the safety standard. He immediately launched an emergency plan to replace the line. A week later, a similar building in the same block caught fire due to aging cables.
Wire aging diagnosis has entered the era of “multi-parameter intelligent evaluation” from “empirical judgment”. The research team of Shanghai Jiaotong University proved through the analysis of 466 on-site aging cables that the laying method directly affects the aging mode-the cable in the pipe is more susceptible to thermal oxidation, while the direct buried cable faces more serious overall degradation.
When multi-dimensional data such as insulation resistance test, ground resistance test, and material analysis are gathered into the intelligent diagnosis system, electrical safety can truly be prevented before it “ignites”.